September 2024 Issue Index
Revolutionising operations
Maptek resource tracking is revolutionising operations at an iron ore mine in South Africa through real-time reconciliation of material quantity and quality.
Anglo American’s Sishen operation is one of the largest open pit mines in the world. Located in the Northern Cape Province of South Africa, Sishen delivers various iron ore products to customer specifications.
Operational efficiency and accurate resource tracking are critical for productivity and profitability. Maptek has played a pivotal role in transforming Sishen Mine operations by implementing advanced tracking and monitoring technologies.
The Maptek–Sishen journey began in 2004 with the introduction of the former MineSuite system to the Dense Media Separation (DMS) plant, providing a foundation for real-time data acquisition and reporting, and improved operational transparency.
Expansion to include the Jig plant and the Modular plant laid the groundwork for comprehensive monitoring across different processing stages. Upgrades between 2018-22 incorporated automated inputs and reconfigured the active web reports platform.
A significant milestone was SAP integration, enhancing data flow and decision-making capabilities.
System robustness was further strengthened with the introduction of Maptek resource tracking and stockpile management in 2024, improving data analytics, real-time monitoring and automated reporting.
Complex value chain
The mine operation is a complex network involving production drills, blasting, load and haul, crushing, pre-beneficiation stockpiling, cyclones, modular DMS, beneficiation plants and shipping logistics to Saldanha Bay port.
Effective management of more than 400 parent processes and 2000 equipment pieces necessitates sophisticated tracking. Maptek solutions provided the requisite functionality for tracking equipment delays and operational metrics.
The control room infrastructure, integral to the monitoring process, expanded from two to ten control rooms, ensuring comprehensive oversight and coordination.
The system operates 24/7/365, on a four-shift system. About 50 control room operators book equipment delays in a 24-hour period, while operational and maintenance managers oversee daily operations, supported by a system analyst.
Data generation and use
Information generation and utilisation at Sishen Mine follow a rigorous process. Data is collected through systemised and manual inputs at eight-hour intervals, validated by shift supervisors.
Data includes production and delay metrics, essential for understanding operational performance. Corrections and updates are handled at various levels, from immediate adjustments by all Control Room Operators to monthly reviews by super users and system analysts for complex issues.
Data generation is easy, but data validation is crucial to sustain any data-driven system.
The reporting mechanism is equally robust, with systemised and emailed outputs facilitating real-time and historical data access. Key performance indicators, time allocation details, production reports and tonnage tracking are meticulously documented.
Integration with SAP and other systems ensures seamless data flow across departments, enhancing overall operational efficiency.
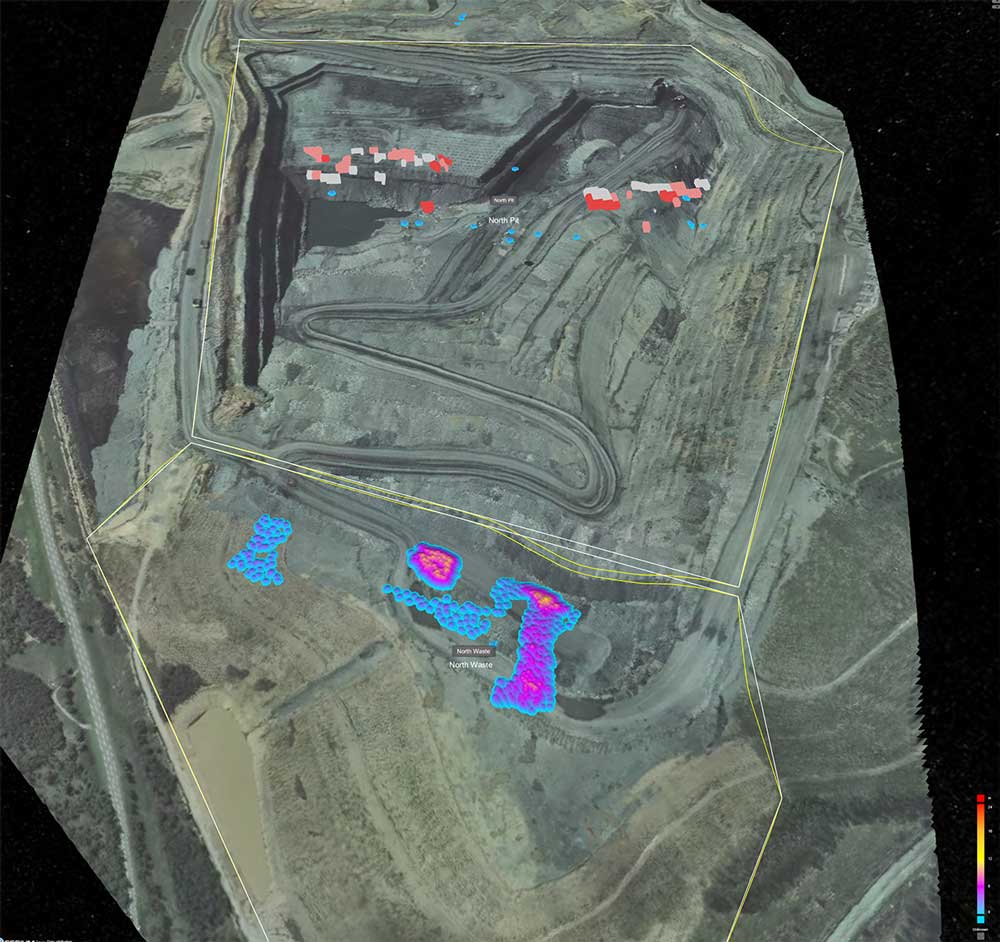
Automation
Material tracking and stockpile modelling have revolutionised the operational landscape. Automating the alignment and reporting of product beds ensures accurate, real-time data flow between Sishen Mine and Saldanha Bay port.
Visual representation of stacked products and their qualities enables accurate reconciliation between stack and reclaim processes.
Automated emails and visual alerts highlight production discrepancies, enhancing accuracy and decision making.
Custom output reports were critical to the system’s success, eliminating the need for manual report creation. This reduced operational bottlenecks and streamlined information flow.
Key drivers to success
Successful implementation at Sishen Mine can be attributed to several key factors:
- Expert personnel: A system analyst with deep operational understanding ensures the quality and accuracy of information, providing continuous training and support.
- Engagement with supervisors and operators: Involving end-users in system design and rollout mitigated change management challenges.
- Comprehensive system integration: Linking processing information with mining, laboratory and logistics data enabled more valuable reporting and decision making.
- Consistency and accuracy: Routine reviews ensured the reliability of information across all departments.
The collaboration between Maptek and Sishen Mine epitomises the way advanced technology can revolutionise mining operations. Through continuous upgrades and a focus on accuracy and integration, Maptek solutions have significantly enhanced mine efficiency and productivity.
Innovative approaches will continue to be pivotal in maintaining competitive advantage and operational excellence in mining.
Thanks to
Anglo American Sishen Mine
- Involving end-users in system design and rollout eased change management and ensured success of a solution that allows Sishen Mine to track equipment delays and operational metrics across more than 400 parent processes and 2000 equipment pieces
- Linking processing information with mining, laboratory and logistics data, and taking advantage of visual representations enabled seamless data flow and accurate reconciliation
- Collaboration between Maptek and Sishen shows how advanced technology can revolutionise mining operations, and provide more valuable reporting and decision making