March 2021 Issue Index
Improve with real-time material tracking
Consistently delivering a correct blend, and keeping track of inventory and quality at all stages of production are universal challenges at mine sites.
Mine value chains are complex and fast moving, making it difficult to accurately track and manage ore.
Each site has different imperatives for blending. Planning becomes more complex depending on the consistency of the lithology and the intended use of the product.
Delivering an overly rich or diluted product unfit for purpose wastes time and money.
Disconnects within data and systems that track inventory have typically resulted in a loss of value through a lack of compliance to plan. These gaps cause delays and operational inefficiencies, and present a risk in contract penalties and under-valuing products.
Maptek MaterialMRT tracks the value of resource, planning and production data along the mining value chain. This integrated enterprise system allows all stakeholders to better understand the factors that impact operational performance in near real time, and in greater detail than previously possible.
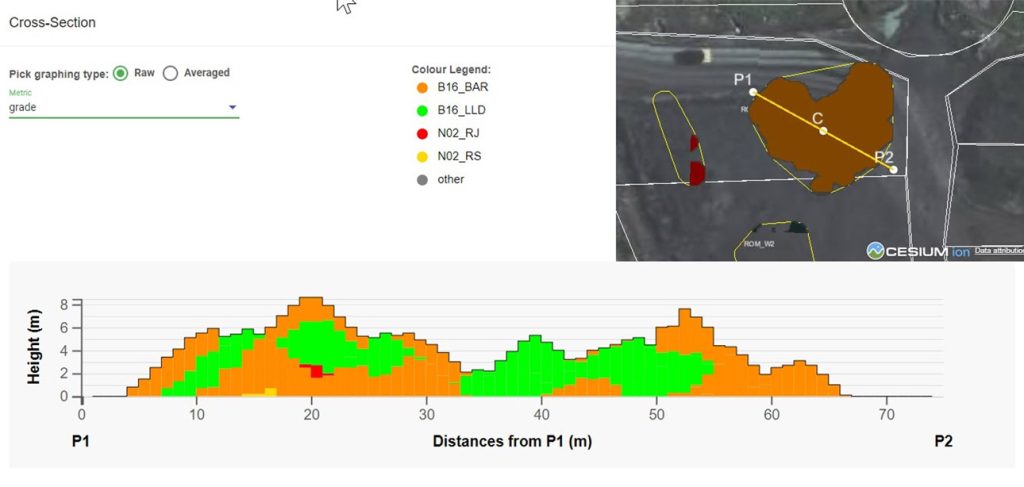
Mining operations benefit from quality and quantity control of material flows from in-situ resource to run-of-mine stockpiles and feed into the plant. This is enabled through a cloud-ready centralised server, with a web-based user interface and a database optimised for storing arbitrary time series geospatial data.
MaterialMRT provides a 3D display, configurable dashboards and data warehouse for custom reporting.
Maptek Group Product Strategy Manager, Mark Roberts says that MaterialMRT is applicable to a wide range of operations.
‘Everyone can benefit from reduced costs, increased revenue and reduced risks of delivery off spec’, says Roberts.
MaterialMRT connects the resource model, mine plan, fleet management, on-belt analysers, survey, laboratory and plant time usage data. It presents a validated, accurate and up-to-date view of the movement and quality of mined material and product as it moves through the value chain.
MaterialMRT provides the big picture on operational performance.
‘The value chain starts with the in-situ resource, where we’ve already made assumptions about the value. Then we blow it up, dig it up, haul it and direct feed it into a plant or put it on a stockpile. By continually tracking the movement and flow of material from in the ground to the plant feed we can now reconcile back to the resource model and mine plan from each stage of the value chain and address issues in the next planning cycle,’ explains Roberts.
Access to accurate, validated data is vital to avoid ambiguity, uncertainty and risk. Better decisions can then be made per shift and in shift.
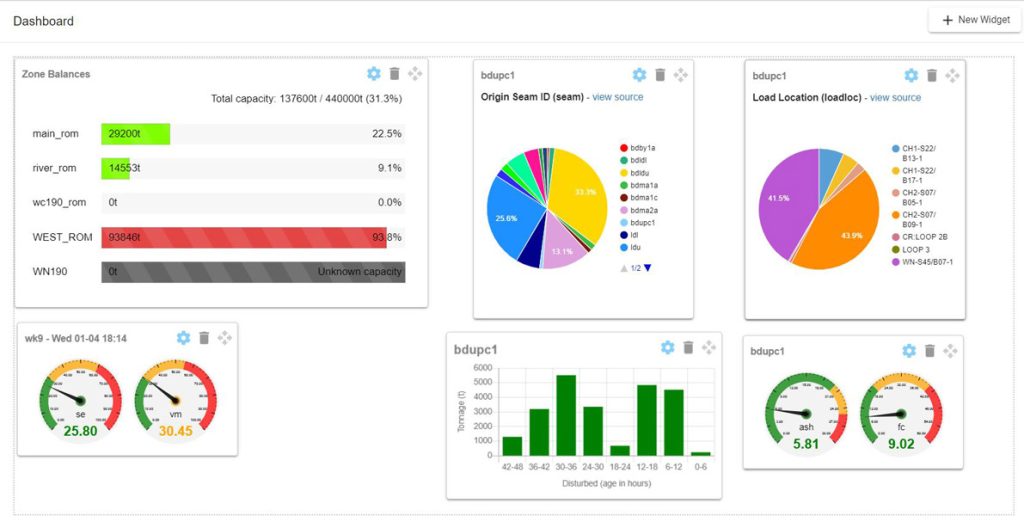
MaterialMRT delivers the current state of material flows and stockpiles through close integration with all critical data sources and systems. This provides a decision support mechanism for most accurately meeting the plant feed plan and product objectives.
‘This support is important for business success. Robust, repeatable and user-independent systems are consistent with a data-driven approach,’ says Roberts.
The outcome is more accurate integrated planning of plant feed so mines can maximise long-to-short term performance in product delivery and plant throughput, thereby maximising value in their resource recovery.
All stakeholders across the mine value chain can now have clear, easily understood information about the objectives, plans and performance of the operation.
- Delivering trackable inventory and reconciliation against the project resource model supports planning and forecasting
- Operations can lower costs through effective feed blend planning, efficient loadout and reduced demurrage fees
- Reduced risk of delivering non-specified product strengthens customer relationships