June 2023 Issue Index
Improving leach pad safety
A monitoring technique using Maptek Sentry safely controls the shape of a secondary leach pad at a copper mine in South America.
This study presents a monitoring technique for performing geometric control over a secondary leach pad construction. Maptek Sentry allows monitoring and characterisation of volume and tonnage to verify design parameters.
Dimensions such as width, length, height and slope angle must be precise to preserve the shape of the deposited crushed material and avoid landslides after the material settles.
Accurate values are needed to determine cubic metres of fill and tonnage of the pile. Existing volume estimates are frequently inaccurate depending on how they are calculated.
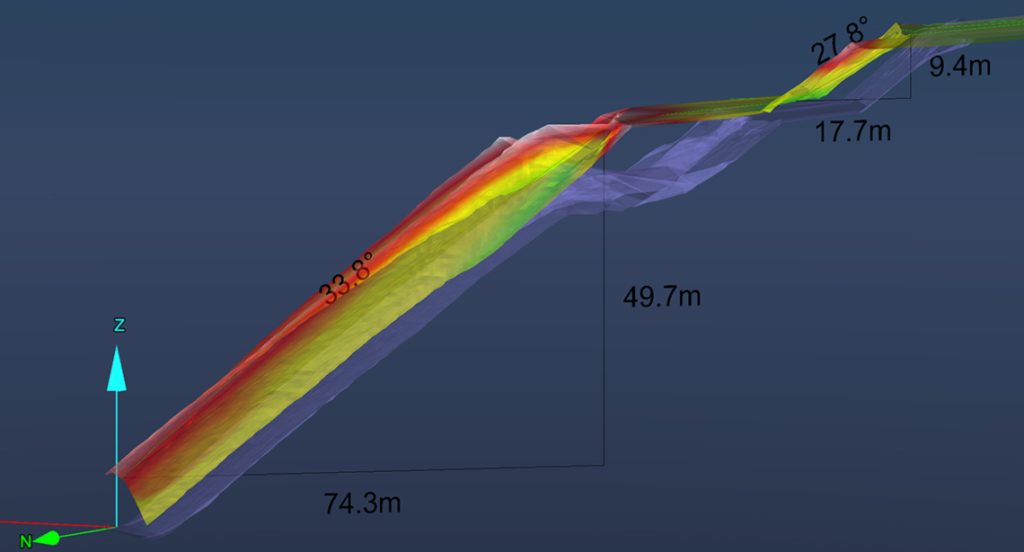
Continuous monitoring of the construction of leach pad cones allows unloading of material to create ‘low’ and ‘high’ zones that respect the design parameters. Real-time geometric control of the pad construction ensures the filling cones are not overloaded, providing greater operational safety.
The cumulative volume of material is measured topographically on a weekly basis, rather than relying on a weight sensor in the spreader.
Design conformance
Maptek Sentry DMS integrates a Maptek XR3-CT MkII laser scanner that captures a 3D point cloud, with Maptek Sentry Field software to display data in real time.
Users can configure monitoring windows to establish alarms that notify by email and text message when there is movement outside the defined range, allowing quick action in response to events of high operational risk.
Processing of the point cloud data and quantisation of the leach pad advance material was achieved with Maptek PointStudio software Design Conformance tools. Compliance was determined between triangulations that were generated daily over a six-week period.
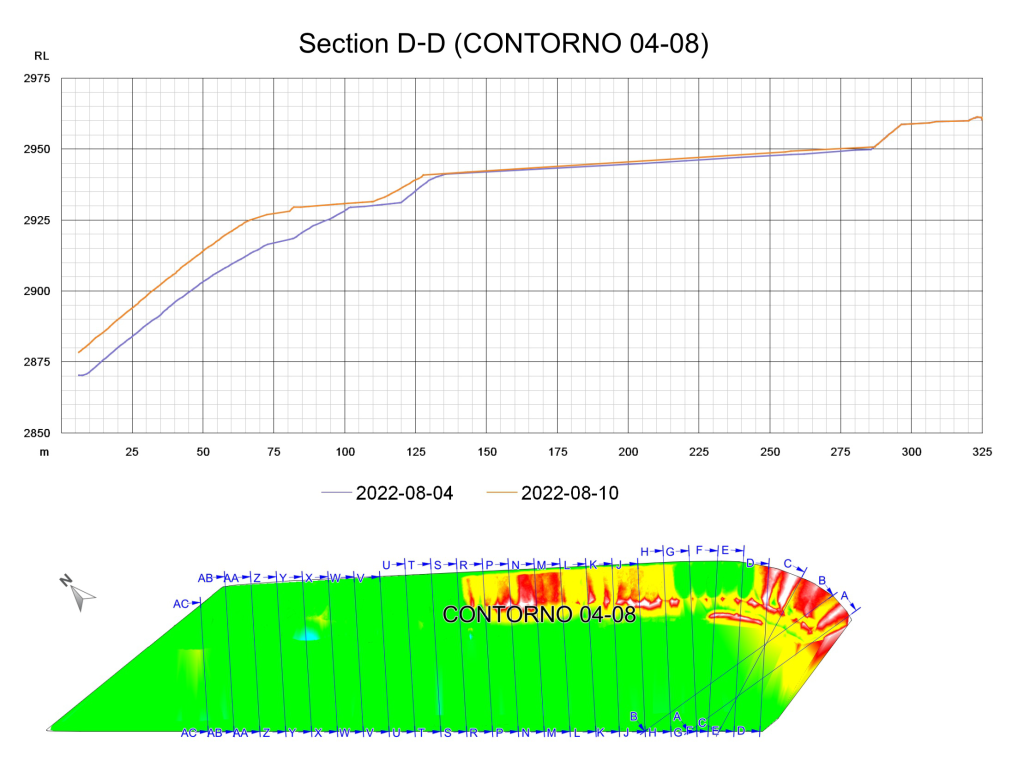
Monitoring results
Data from the most representative week of the Sentry monitoring period were selected for this study.
Sentry Field automatically alerted users to displacements of built cones and enabled the spreader operator to observe the material discharge point. Because discharge stop alerts were also provided, additional personnel were not required for geometric control and stability.
Geometric control of material discharge requires knowing the slope angle of the discharge cone and the heights of the cone and low zone blind spots. In one profile, PointStudio showed slope angles of 33.8° for the cone and 27.8° for the low zone, while heights were 49.7m and 9.4m, respectively (Figure 1).
The ability to observe material discharge minute by minute, along with managing the slope angle and covering the discharge blind spot, provides greater control and safety to mining operations.
Unloading volumes and tonnages were tabulated in the unloaded and low cone advance zones. In Figure 2, areas of the triangulated stockpile coloured in red and white correspond to the highest concentration of material. Red indicates an accumulation of material of more than 5m in one week and white indicates an accumulation of more than 10m.
Geometric control
Monitoring the construction of secondary leach pad cones has shown that the design parameters can be correctly determined, providing reportability, quantification, calculation and geometric control.
Importantly, this was achieved without exposing the equipment operator to the deposition area.
Ensuring operational safety of personnel was important.
Specific monitoring must be carried out for deposits of already leached material because the granulometry of the mineral varies. Particulate material, with lower slip resistance is generated, affecting the stability of the pile. In addition, the humidity level is key to maintaining particle cohesion.
With the stability of the pile depending on multiple factors, this study has focused on the monitoring process for material deposits and how that contributes to the reportability and calculation of volumetrics and geometric control of the pile.
The technique used in this study provides a remote, safe, autonomous and sustainable way to manage blind spots when an operator is building cones and/or slopes, avoiding landslides after the particulate material has settled.
Based on a paper presented to Geotechnical and Hydrogeology Symposium, Lima, Peru
- Multiple safety and operational factors must be considered when designing and managing secondary leach pads
- Continuous, remote monitoring avoids material overloading and highlights hazards such as blind spots
- Maptek Sentry provides operators with a safe and autonomous way to build and monitor leach pads, avoiding landslides after particulate material has settled