June 2023 Issue Index
BlastMCF – Ahead of the blast curve
Maptek has developed a new machine learning method for blast design which allows operations to do more with less.
Automation, data analytics and optimisation are key industry trends. In reality they mean doing more and better, while using less resources. The continuing explosion of mine technical data requires solutions to harness this data, allowing miners to derive optimum value from it.
Traditional blast design is being challenged on several fronts. The engineering intensive methodology is not practical given the shrinking pool of mine professionals, and a just-in-time philosophy is not consistent with the drive for automation. A more automated approach is needed to generate scenarios that are critical for evaluating the interrelated factors influencing blast performance and to better understand them.
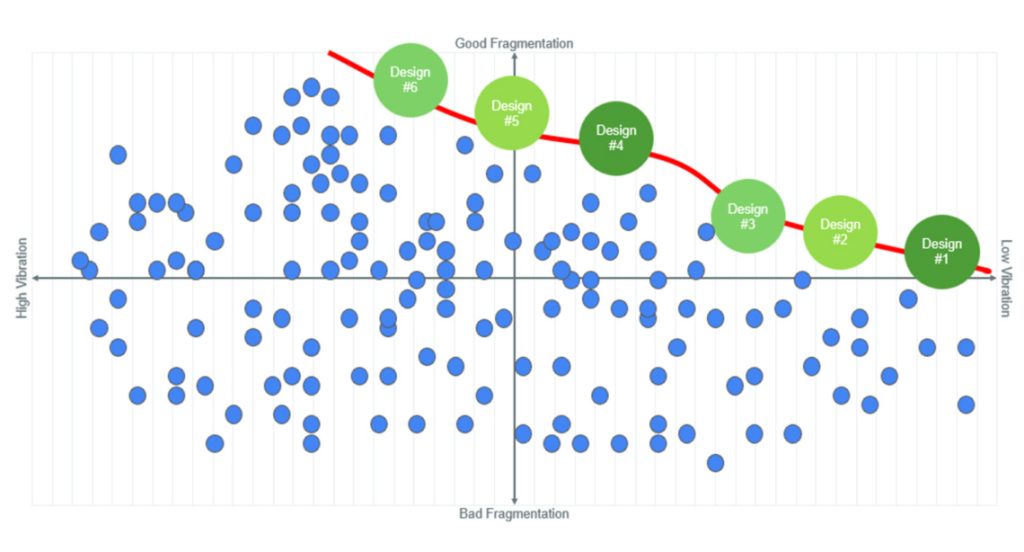
Maptek BlastMCF uses a customised genetic algorithm, drawing inspiration from the principles of natural evolution to solve complex problems, which provides a powerful and flexible approach to optimisation. It will enable engineers to perform more scenario analysis to objectively validate and verify design concepts quickly, thereby benchmarking the critical factors that impact blast performance specific to localised conditions.
A significant advantage of BlastMCF over traditional design tools is the automated generation of drill pattern, per hole charge plan and timing in a single step. Even for designs that comprise different lithological domains, running separate processing jobs for each domain and using the resulting design from the first domain as an input to the next, the process is still simple.
Leveraging the differences between possible design options, BlastMCF converges on the best possible solutions considering competing design objectives such as cost, fly rock, fragmentation, powder factor and vibration.
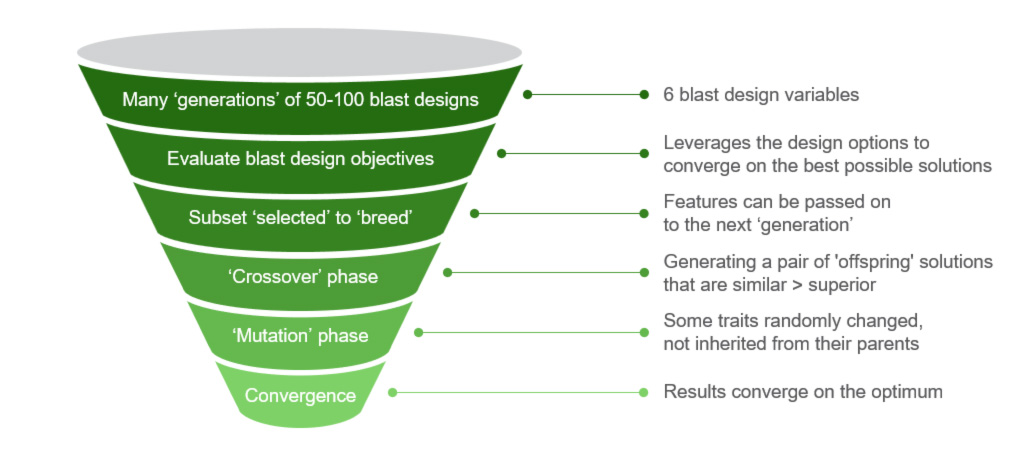
Optimising competing blast objectives will no longer require brute force by engineers, allowing optimal blast design outcomes to be more accessible. A cross-section of possible solutions is available for the engineer to compare and better understand the trade-offs between various design parameters.
Integrating cost, fly rock, fragmentation, powder factor and vibration models into the blast design with BlastMCF will enable blast outcomes to be targeted with greater precision. Given their interconnectedness as part of upstream and downstream processes, this will maximise the value realised.
BlastMCF delivers an innovative machine learning approach to optimising blast design, allowing for consistent repeatable designs that can be evaluated alongside short and medium term planning workflows.
Engineers retain control of the design without needing to spend days going through multiple potential solutions, and cloud computing is leveraged for running optimisations faster than on local machines. Even complex results are generated within minutes, improving the ability to review scenarios and improve designs under production pressures.
BlastMCF can help mines save thousands of dollars on a per blast basis without compromising safety or productivity. Harnessing automation, data analytics and optimisation for the best blast performance supports engineers to transform their drill and blast design practices and change the way mining is done, forever.
- BlastMCF leverages evolutionary computing techniques to transform the engineering intensive task of creating individual, just-in-time blast designs
- Optimised, automated creation of blast designs references fragmentation, vibration and fly rock models as well as objectives like costs and powder factor
- Generating optimum blast designs early allows operations to analyse as part of short and medium term planning, adding value to the entire mine operations workflow