June 2021 Issue Index
Controlling stockpiles
A new Maptek solution helps schedule and control the stage cycle of stockpiles to better manage space, grade and inventory to deliver product on time every time.
Large mining operations face a common challenge of managing stockpile space while simultaneously ensuring that the required product consignments are being delivered. Stockpile builds depend on availability, and when space is limited it is difficult to avoid costly rehandle.
Maptek StockpileMRT helps manage and monitor available space, tracking where material is moved to and how it is reintroduced into the environment.
StockpileMRT provides a clear graphical schematic of the stockyard, stockpile pads and builds.
The concept is similar to the well-known London Underground, where commuters use schematic maps that are neither geographically precise nor to scale.
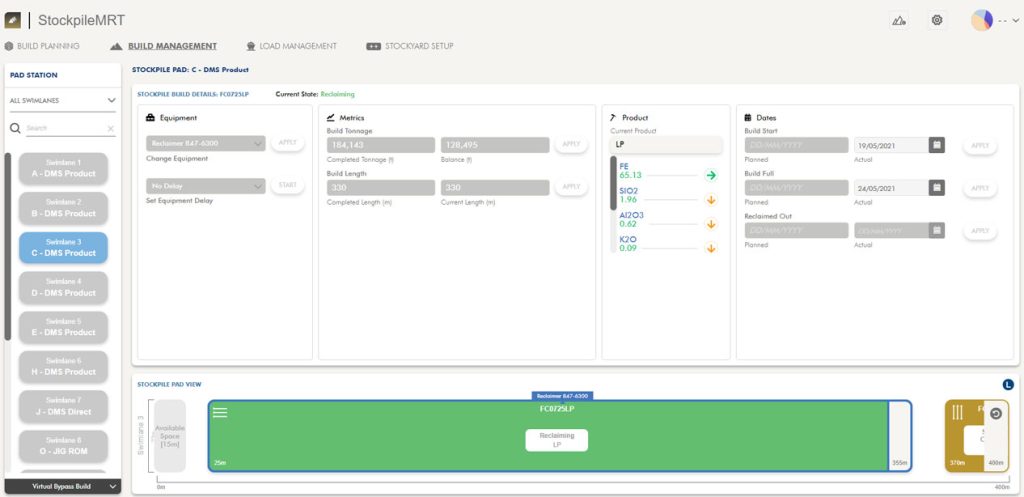
At a mine, planners must decide how much material is allocated to build stockpiles, so that grade and inventory targets are achieved. Completed stockpiles must have consistent grade and composition, which requires careful scheduling of the stage cycles of stockpile builds to maintain operational control from survey to laboratory results, to load-out.
StockpileMRT supports the specific stages that stockpiles cycle through, tracking the status of each stockpile based on inventory and grade.
Automated interfaces with control and instrumentation, laboratory information and train management systems provide users with near-live status and measurements.
A cloud-ready server and advanced web-based user interface provide near-live views and reporting to all stakeholders in the planning, building and loading processes.
StockpileMRT supports more informed value-in-use decision making. Take a manganese mine for example, that prepares run-of-mine stockpiles, feeding the processing plant with ore at target composition of grade and contaminants.
From the plant, physical and source characteristics are sorted and allocated to existing or new truck tips and fines stockpiles that are then blended into intermediary or product stockpiles ready for delivery. Once a particular stockpile is full, a new one is generated and enters the process, or a depleted stockpile begins the process again.
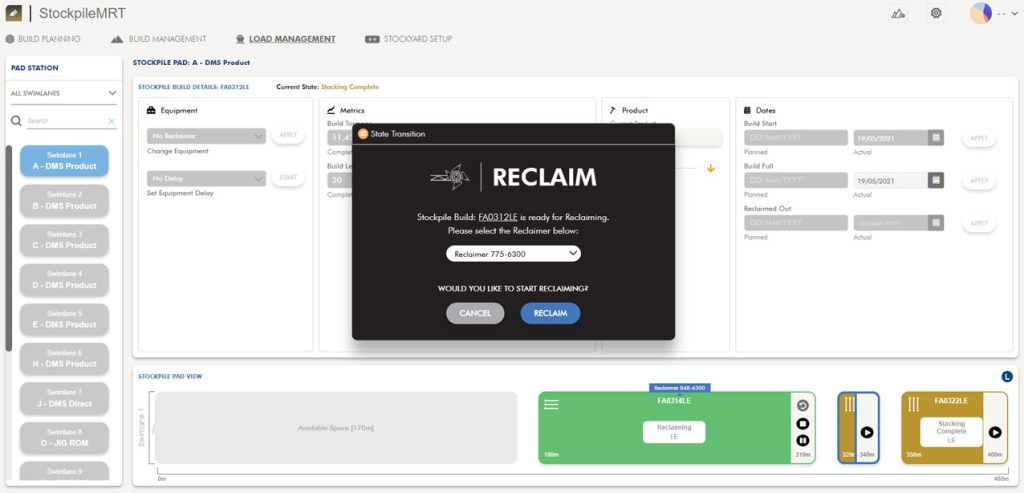
StockpileMRT enables more accurate planning and forecasting of inventory by increasing the visibility of grade and tonnes currently available on stockpiles, or that will soon be available through the upstream mining and plant processes.
Near-live accurate inventory and grade composition data is delivered throughout the stockpile stage cycles, and each re-handling event is tracked. This helps minimise costs that arise from time delayed in-shift decision making, such as around train loading, blending profiles and the reclaim process.
StockpileMRT ensures optimal utilisation of available space, and that value is preserved by avoiding delivery of variable or off-spec product. Additionally, it provides the ability to improve the price premium by reducing final product quality variability and bias.
- A graphical schematic of stockyard, stockpile pads and builds helps operations schedule and control material movement and deliver correct product to customers
- Automated interfaces with control and instrumentation, laboratory information and train management systems provide near-live status and measurements
- Delivering near-live accurate inventory and grade data across stockpile stage cycles and tracking re-handling events minimises delays and associated costs
Maptek Connect 2021
On May 19 our customers, partners and industry experts provided their insights around the latest mining challenges and shared their tips for success.
Recorded sessions are now available to watch on demand.