June 2019 Issue Index
Digitalisation of drill and blast
Barrick Pueblo Viejo has improved day-to-day operations and provided greater business intelligence for future mining excellence through implementing Maptek BlastLogic.
Innovation through digitalisation and technology is a key focus for Barrick. This is strongly evident at its Pueblo Viejo operation, an open pit gold mine in the Dominican Republic, particularly in the drill & blast department.
The Maptek blast design and reconciliation solution, that includes BlastLogic and Vulcan Drilling Designer, has given Pueblo Viejo a single platform to manage its drill & blast process from design to performance measurement. Integrated tracking of vibration, fragmentation, performance, cost and inventory of each blast facilitates continuous improvement from blast to blast and informs future planning.
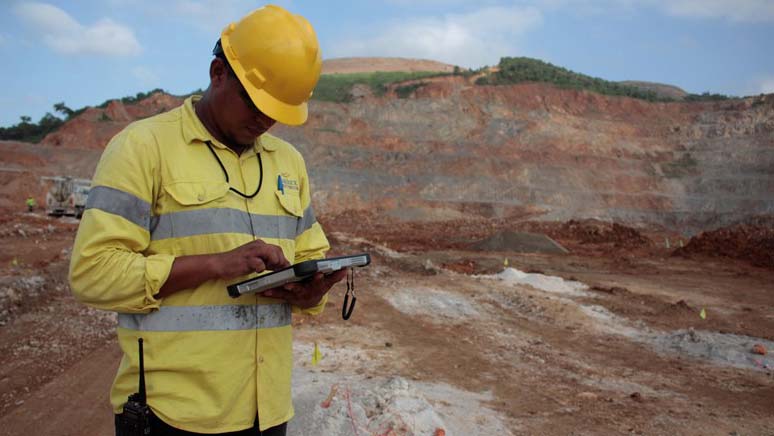
‘Digitalisation is key to continuous improvement. Automating data generation enables innovation around operational processes that optimise the business’, said Alejandro Rosario, Senior Drill & Blast Engineer at Barrick Pueblo Viejo.
Direct benefits include increased drilling accuracy, efficient back analysis, enhanced online data management, cost savings for explosives, and a faster and easier improvement process.
‘As results of each blast are fed back automatically, we spend less time figuring out what we need to change in our designs. This enables us to apply improvements in real time’, said Rosario.
Prior to the implementation of BlastLogic, blast data existed in multiple silos. All machinery collected and compiled drill information, but a lot of blast data was recorded by hand and kept separate from the drill data. Accessing the disparate data was difficult and analysis was time-consuming.
The BlastLogic database now contains all related drill & blast data, enabling faster, easier, more effective analysis.
Importantly, digitalisation enables benchmarking so that the effect of changes can be measured. For example, with all drill data integrated to blasting results, improvements in accurate charge placement are easily realised, delivering better fragmentation. Blasting can be performed with smarter and safer sequences.
Real-time feedback of an electronic detonator misfire allows immediate identification of issues and avoids unexpected outcomes. Accuracy is critical for safety in dealing with explosives.
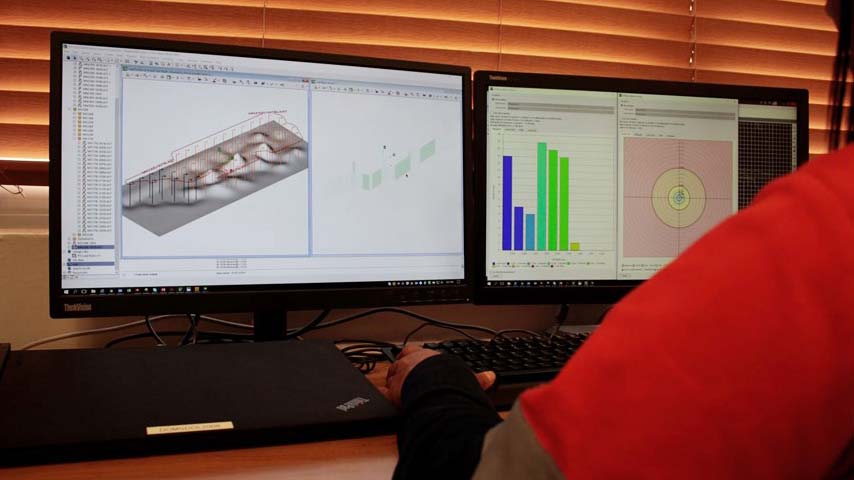
The administration of tasks and resources has also been enhanced, data analysis time has been reduced, and business intelligence can be applied to reduce costs and time spent. This has been achieved by substantially shifting the amount of engineering time from data entry, formatting, reporting and meetings to planning, compliance and improvement.
Access to digital drill and blast data allows easier communication of accurate information between departments. Data integration has provided:
- Detailed control of drill & blast KPIs (daily, weekly, monthly, etc.), with parameters such as total metres drilled, re-drilling, over-drilling, penetration rate, powder factor, fragmentation, total explosive usage, tonnage removed.
- The ability to audit contractors and the overall blasting process.
- Synchronisation of drill & blast tasks into a single platform, with pattern design, charge plan, tie-up design, drilling, QA/QC, observations, fragmentation and vibration control.
- Data and process transparency, including online access for managers and an increased ability to check indicators.
- Correlation of data in 3D for simple analysis and summary dashboards to track technical, economic and operational opportunities for drill & blast. For example, drill depth and collar accuracy, redrills, over/under drilling and associated costs.
Rosario concluded, ‘We ultimately chose BlastLogic for more than just the software capabilities. Along with the technology, we have access to a phenomenal support team helping us customise the platform specifically for our operations. We are paying for more than a fixed solution, one that can grow with our needs and is backed by excellent customer service.’
Thanks to
Alejandro Rosario
Senior Drill & Blast Engineer
Barrick Pueblo Viejo Mine
- When blast data exists in multiple silos it is difficult to access and analysis is time-consuming
- Integrated tracking of vibration, fragmentation, performance, cost and inventory of each blast facilitates continuous improvement from blast to blast
- BlastLogic delivers more than a fixed solution, it grows with customer needs and is backed by excellent customer service