December 2023 Issue Index
Accounting for loss and dilution
A solution for estimating loss and dilution that takes into account product recovery, material handling costs and minimum mining unit proves effective for complex projects.
Traditional approaches to predicting ore loss and planned dilution in open pit mining work well for broad planning, but more advanced techniques can be beneficial when working with challenging deposits such as narrow vein and disseminated orebodies.
Best practice requires engineers to consider recoverable metal, extraction costs, and the minimum selective mining unit (SMU).
Common methods include:
Standard loss and dilution factors based on metal grades, not accounting for variations in mineral dissemination. Often applied at the pre-feasibility stage or for high level studies, in practice this approach often underestimates actual loss and dilution.
Reblocking the resource model to match the SMU. This conservative method provides more localised estimates that better reflect variability within the mineralised material, but can overestimate loss and dilution in areas of complex mineralisation.
Manually defining SMU compliant ore/waste boundaries by reviewing grades on each mining bench/flitch.
While effective, this is a subjective, repetitive process that does not always take into consideration the optimal grade cut-off.
Maptek customers have identified a need for user-friendly solutions that streamline and standardise the process for predicting ore loss and dilution, while enhancing accuracy for complex deposits. Planners also want to be able to rapidly generate multiple scenarios for equipment trade-off studies, especially when assessing the impact of bulk or selective mining.
A unique approach to tackle these challenges harnesses the capability of the Vulcan Grade Control Optimiser. This specialised tool was initially designed to optimise material categorisation within individual blasts as part of the production grade control process. It then became evident that the use could expand to cover entire mining projects.
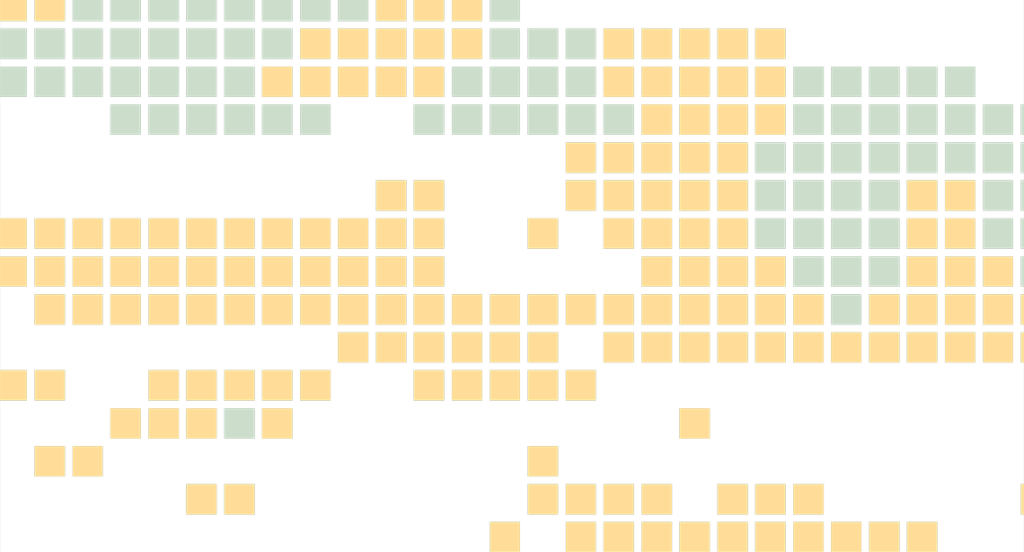
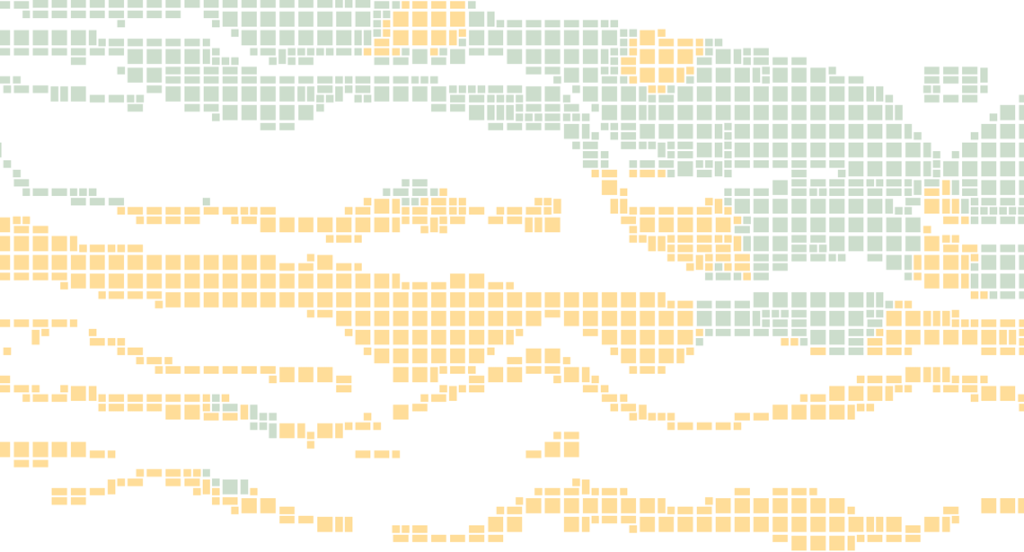
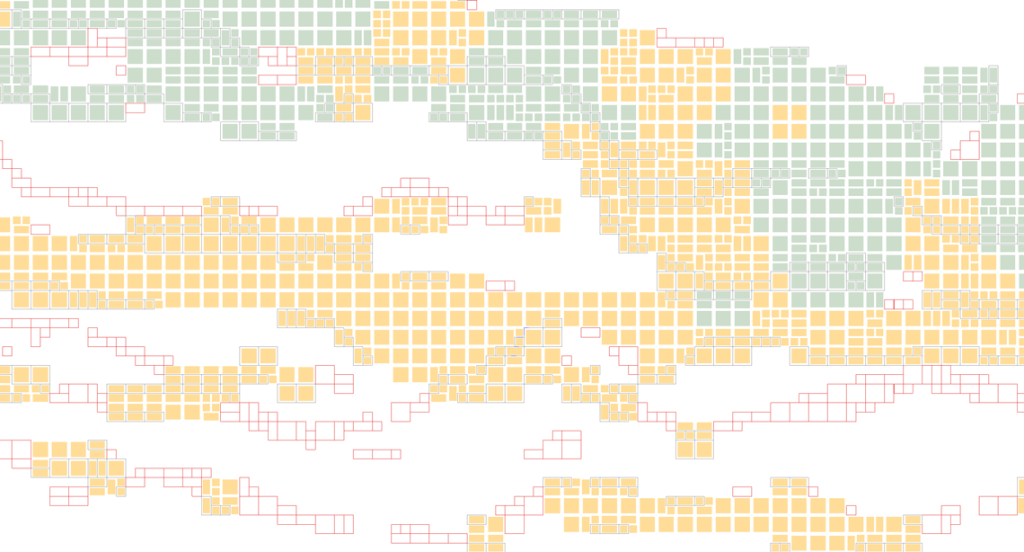
Comparison of the optimal material destination on a single flitch. Original resource model (top), traditional reblocking approach (middle) and GCO result (bottom). Colours represent optimal ore destination (orange = heap leach & green = CiL)
Grade Control Optimiser is batch run on individual mining benches or flitches, with the results supporting decision making in strategic and medium-term loss/dilution studies.
The solution can quickly identify areas of ore loss and diluting blocks and store the results within a single block model. Predetermined minimum mining width (or SMU), destination specific material handling costs, and destination specific product recoveries can be considered as part of the process.
Beyond classifying blocks as ore or waste, the output also identifies the most profitable processing destination. It assesses the net value of each block by assuming it can be sent to each specified destination before determining the most profitable and mineable option that complies with the initial SMU constraint.
Customers who have embraced this approach report that it is user-friendly and offers greater transparency for auditing.
The results obtained from Grade Control Optimiser based loss and dilution studies can seamlessly integrate into subsequent activities, including pushback design, production scheduling and reconciliation studies.
- Creative application of grade control optimisation tools proves effective at excluding impractical mining areas as part of loss and dilution studies
- Product recovery, material handling costs, minimum mining width and profitable processing destination are accounted for in the new methodology
- Customers report that the optimisation approach is user-friendly and offers greater transparency for auditing